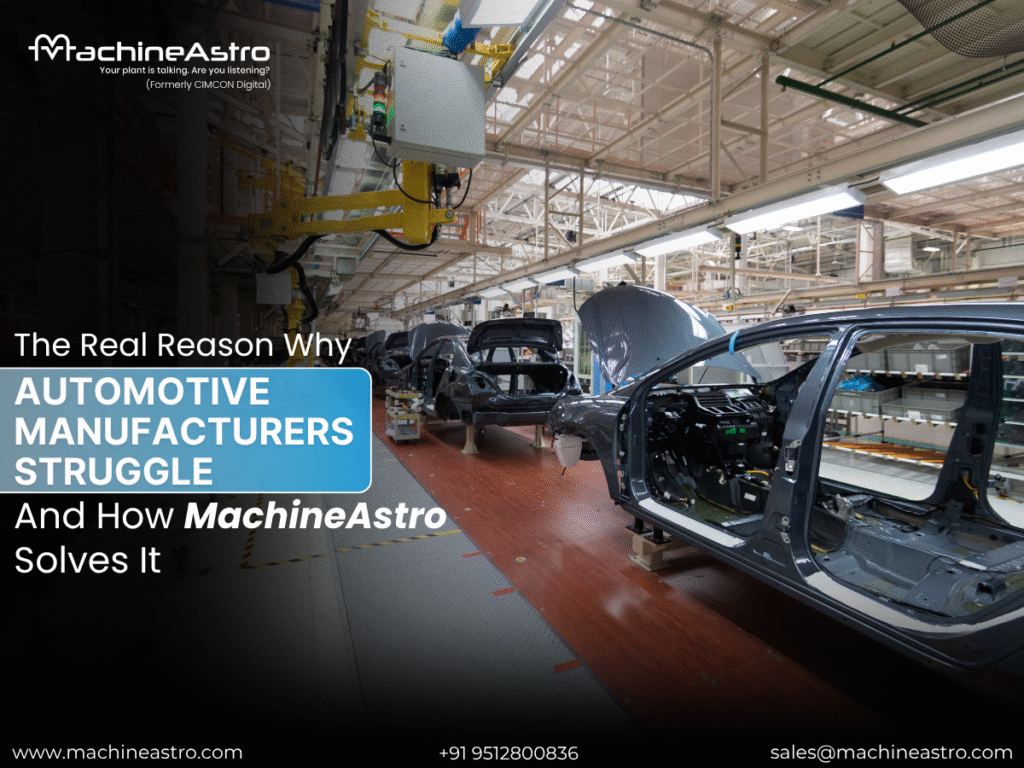
The automotive manufacturing industry is evolving rapidly, but one reality hasn’t changed: unplanned downtime, rising maintenance costs, and energy inefficiencies are still among the biggest obstacles to achieving production targets and profitability.
In today’s competitive environment—where every minute of production counts—these challenges are more critical than ever. Here’s what’s really happening on the ground, and how MachineAstro’s predictive maintenance and energy analytics solution empowers automotive manufacturers to overcome them.
🚨 Challenge 1: Unplanned Downtime Disrupts Production
The Reality: Even a single unexpected equipment failure in a press shop, weld line, or paint booth can halt an entire production line. Studies show that each hour of downtime can cost automotive manufacturers anywhere between ₹5 lakh to ₹20 lakh, depending on the plant and the model being produced.
What causes it?
- Bearings wearing out in conveyors or robots.
- Imbalance or Mechanical faults like structural, Alignment, Rotational, Mechanical components, gearbox teeth related issue.
- Overheating of critical machines.
Why traditional maintenance fails:
Conventional time-based maintenance can’t predict when failures will happen. Inspections might miss early warning signs. By the time an operator hears a strange noise or notices vibration, the damage is often already done.
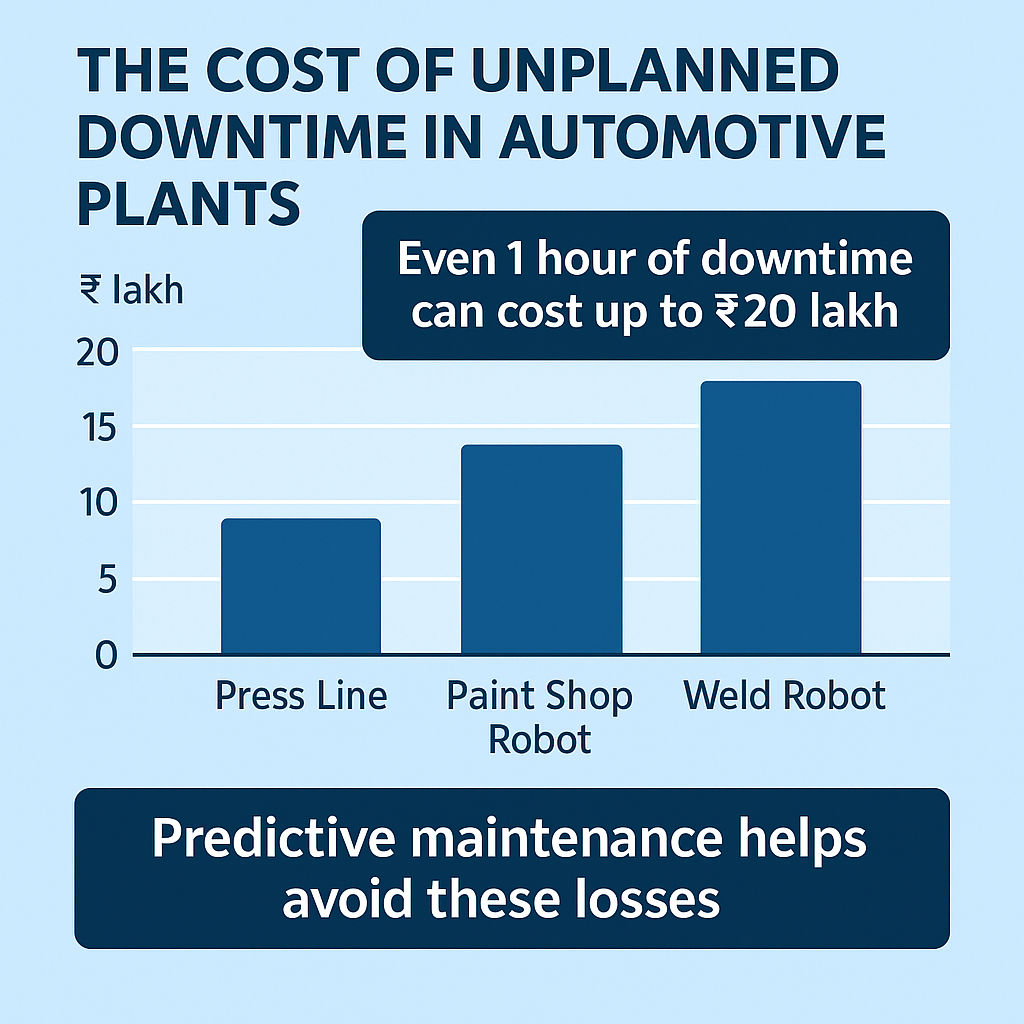
- Our Solution:
VIBit condition monitoring sensors continuously track vibration and temperature on critical assets. Our platform detects early-stage issues like bearing defects, structural,
Alignment, Rotational, Mechanical components, gearbox teeth related issue, [A1] alerting
your team before they lead to costly breakdowns.
🚨 Challenge 2: High Maintenance Costs
The Reality: Automotive plants spend crores every year on reactive repairs, emergency parts replacement, and unplanned labour eating into margins.
Why this happens:
- Repairs are done only after failures occur.
- Frequent emergency stoppages increase overtime costs.
- Spare parts inventories swell due to uncertainty.
Our solution:
AI-based predictive analytics help you transition from reactive to proactive maintenance. By knowing which machines need attention, you can plan repairs during scheduled downtime, optimize spare parts inventory, and avoid unnecessary maintenance on healthy equipment—cutting maintenance costs by 25-40%.
🚨 Challenge 3: Invisible Energy Waste
The Reality: Energy is often the second-largest cost in an automotive plant after raw materials. Yet, many manufacturers lack visibility into where and how energy is wasted across equipment and lines.
Typical issues include:
- Motors running at inefficient loads.
- Leaks in compressed air systems.
- Whenever there are mechanical faults, energy consumption increases—for example, misalignment also causes higher-than-normal energy use.
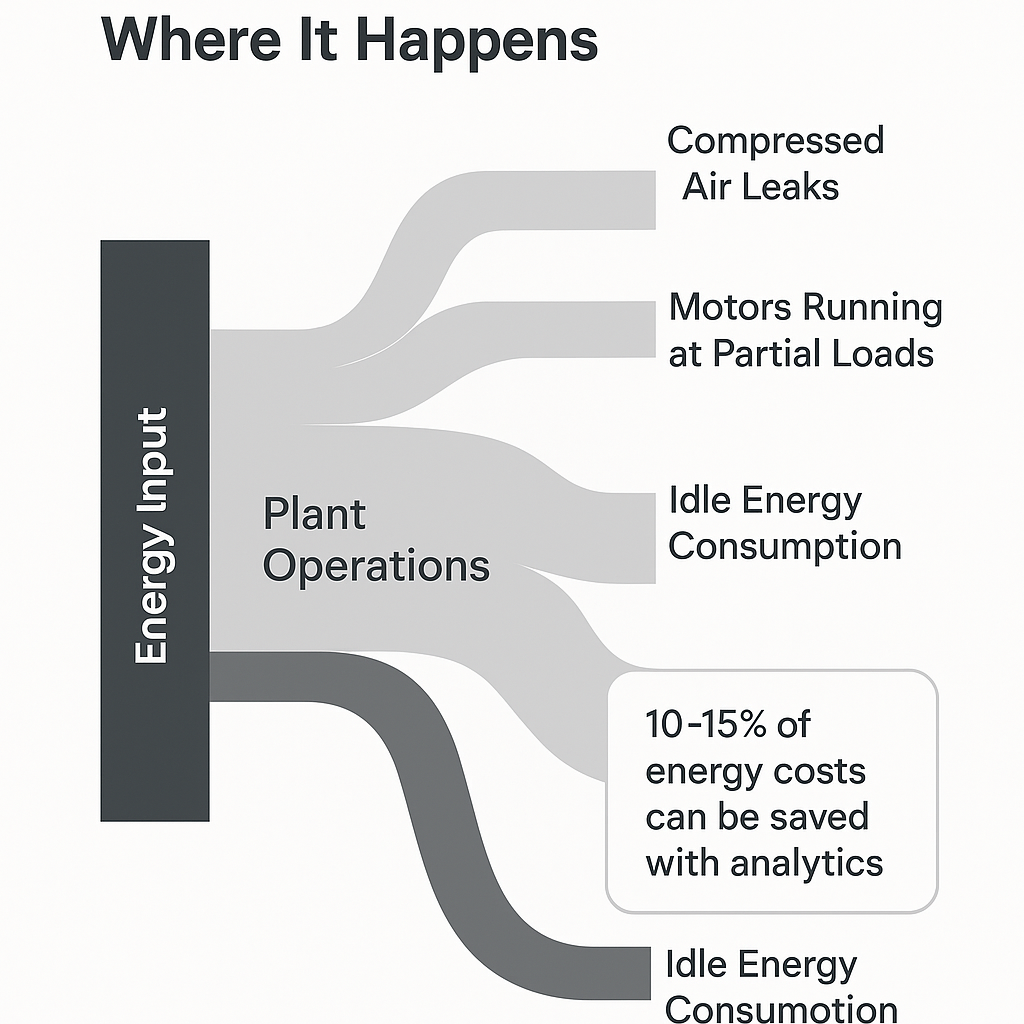
Our Solution:
MachineAstro’s energy analytics measure and analyze energy consumption patterns at the machine and line level, identifying inefficiencies and enabling targeted interventions. Plants using our solution have reduced energy costs by 10-15%, while improving sustainability metrics critical for meeting corporate carbon-reduction goals.
🚨 Challenge 4: Lack of Real-Time Insights
The Reality: Many automotive manufacturers still rely on manual inspections or scattered data sources, making it hard to get a clear, real-time picture of equipment health.
Why it matters:
- Operators and managers make decisions based on incomplete information.
- Slow response times mean small issues escalate into bigger problems.
Our Solution:
iEdge360 unified dashboard centralizes real-time condition data from all monitored assets, providing actionable insights to plant managers, maintenance teams, and leadership. Our platform supports mobile alerts, trend analysis, and customizable reports to enable fast, informed decision-making.
The MachineAstro Advantage: Transform Your Automotive Plant
By tackling these challenges head-on, our predictive maintenance and energy analytics solution enables automotive manufacturers to:
✅ Reduce unplanned downtime by up to 60%.
✅ Lower maintenance costs by 25-40%.
✅ Improve energy efficiency by 10-15%.
✅ Increase overall equipment effectiveness (OEE) and plant productivity.
✅ Enhance sustainability and meet carbon-reduction commitments.

With MachineAstro, you don’t just collect data—you turn it into powerful insights that transform your operations.
MachineAstro's Generative AI-Based Virtual Assistant that will Transform Manufacturing Decision-Making
AI Personal Assistant – MUNI
Muni the AI personal assistant brings game-changing features that make talking to your machines as easy as asking a question. Whether you’re on the shop floor, in maintenance, or managing performance remotely, Muni is now faster, smarter, and always by your side.
Voice-Powered Conversations
Contextual Memory
Smarter Data Access
24/7 Intelligent Support
AI Chatbot – SARATHI
Get ready to elevate your customer support with CIMCON Sarathi, our state-of-the-art chatbot designed to enhance your understanding and management of sensor technology. Sarathi isn’t just a chatbot; it’s your 24/7 digital support agent, equipped to handle all your needs with precision and efficiency.
Comprehensive Product Information
MEMS Technology Insights
Effortless Data Exporting
On-the-Spot Troubleshooting
Conclusion: Build a Resilient, Efficient, and Sustainable Future
The automotive industry is entering a new era of electrification, digitalization, and sustainability. But without a strategy to eliminate downtime, cut maintenance costs, and optimize energy use, manufacturers risk falling behind.
MachineAstro is here to help you stay ahead—by keeping your machines running, your costs under control, and your energy use smart. Let’s future-proof your plant together.
Contact us today to learn how MachineAstro can transform your automotive manufacturing operations.